Imagine a scenario where a robot could self-assemble itself – thus cutting human effort for the same. Recently, MIT researchers have made great strides in the direction of developing robots that could effectively and inexpensively manufacture almost anything, even objects that were considerably larger than themselves, such as automobiles, buildings, and larger robots. The most recent accomplishment is detailed in a paper by professor and Center for Bits and Atoms (CBA) Director Neil Gershenfeld, doctorate student Amira Abdel-Rahman, and three other authors in the journal Nature Communications Engineering.
Robots that can put together structures on their own are called self-assembling robots. Many tend to believe that they are self-building robots, which is a legitimate interpretation of the phrase ‘self-assembling’, but it is not what people in the robotics industry mean.
The team acknowledges that it will be years before they achieve their real goal of a completely autonomous self-replicating robot assembly system that is capable of both planning the optimum building sequence and creating larger structures, including larger robots. However, the new research makes significant progress in that direction by figuring out difficult problems like when to produce more robots, how big to make them, and how to coordinate swarms of robots of various sizes to construct a building effectively without colliding with one another.
This advancement draws on years of research, including various studies showing that deformable airplane wings and working race cars could be put together from small, identical lightweight bits and that some of this assembly work might be done by robots. By demonstrating both the assembler bots and the components of the structure being built can be made of the same subunits and that the robots can move autonomously in vast numbers to complete large-scale assemblies swiftly.
MIT’s new self-assembling robot technology follows a similar assortment of small identical subunits called voxels (the volumetric equivalent of a 2-D pixel) to create huge, useable structures as in earlier tests. This time the team has created advanced voxels where each can transfer both power and data from one unit to the next, unlike the mechanical structural previous voxels. This might enable the building of structures that can not only withstand weights but also perform tasks, such as lifting, moving, and manipulating materials, even the voxels themselves.
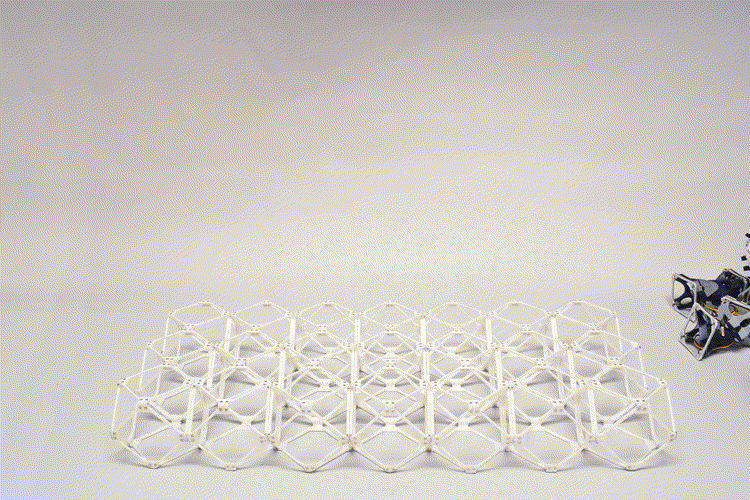
The robots themselves are made up of a string of many voxels linked end to end. These can migrate like inchworms to the desired position, where they can grasp another voxel using attachment points on one end, connect it to the developing structure, and release it there.
Earlier, an MIT team was developing ElectroVoxels, which are tiny, intelligent, self-assembling robots created for space. These robots were tested on NASA’s vomit comet, a large padded airplane with the seats removed for the purpose of giving scientists and pilots a brief moment of zero gravity during looping parabolic flights. The goal of this research was to employ them as unique tools, reorganize mass for spinning motions that would provide a kind of artificial gravity by centrifugal force, or put mass in the way of a potentially harmful solar flare.
Read More: MIT Researchers Solved Differential Equation Problem in Liquid Neural Network
While previous systems designed by the institution could theoretically build arbitrarily enormous structures, MIT warns that once the size of those structures reached a certain threshold in relation to the size of the assembler robot, the process would become undeniably impractical due to the ever-longer journeys each bot would have to traverse to transport each piece to its destination. This also caused path planning complexity. In other words, these systems were certainly an upgrade from the conventional monolithic robots (competent but rigid) and modular robots (flexible but less capable). However, because their numbers and sizes were fixed, scaling led to decreased performance and throughput.
When the voxels became available, the bots could determine if it was time to build a larger version of themselves that could travel farther and faster. While parts of a building with lots of fine detail may need more of the smallest robots, an even greater structure might need yet another similar stage, with the new larger robots generating even larger ones.
The new voxel-based robot system has the ability to assemble robots sequentially, recursively, and hierarchically to create larger robots. To do this, the construction is discretized into a series of uncomplicated, basic building parts that can be rearranged to generate a variety of capabilities. The discretization makes the coordination, navigation, and mistake correction of the swarm considerably lot easier. The component composition is assisted by an algorithm to assemble the building blocks into swarms and strategize the best possible construction journey.
The hardware is based on an earlier system that used passive structural lattice voxels as a foundation for the mobility of specially designed inchworm robots that could place and rearrange additional voxels. Through targeted registration to the underlying lattice, coupling voxels with robots creates a material-robot system that enables the exact assembly of massive structures using simple robots. The new system improves the connection between the material-robot system by developing a modular robotic toolkit with active lattice voxels serving as the main structural building elements. When these active voxels are integrated with actuators, control, and power, they enable novel capabilities such as robotic self-replication and hierarchical robot construction.
Read More: Humanoid Robots: Hype for Economic Gains or threat to Humans?
The six sides of the voxels were created by laminating an acetal face to a printed circuit board (PCB) substrate. These sides are later joined together to form the whole unit cell, which includes soldered intravoxel electrical connections and epoxy reinforcement. A 1.6 mm FR4 substrate and 1oz copper layers were used in the printing of voxel circuit boards using PCBWay custom prototyping. A Trotec Speedy-100 Flexx was used to laser cut the acetal faces, and Loctite SF-770 primer and Loctite 401 adhesive were used for laminating the acetal faces to the voxel circuit boards.
Power, ground, and a single serial communication line are routed through each voxel face using a pair of 4.7625 mm 3.175 mm (3/16 in. 1/8 in.) magnets of opposite polarity to create an orientation-independent structural connection, while a 6-pin spring-connector creates a hermaphroditic interface for the three electrical circuits. The maximum transmission capacity for a face-to-face connection is 8 A at 10 V and 50 N of tensile force. The structural-robotic system is then finished with supplemental active components, including an ESP32-based microcontroller with a 7.4 V lithium polymer battery pack, two rotary actuators where an elbow rotates parallel to the plane of attachment and a wrist that rotates perpendicular to the attachment plane, as well as a gripper made to clamp lattice components for placement, mobility, and assembly.
The voxel-based robot assembling algorithm was governed by two conditions. First, following assembly, the new robot has to be able to move freely. Although this requirement may seem unimportant, the nature of the magnetic connections prevents assembling flat on the lattice substrate and then lifting the finished robot into place. In order to get around this, child carrier robots are built from a foundation that consists of a control voxel and a gripper that can attach to the lattice.
Second, the gripper can only directly operate the base voxels, control and power voxels, and elbow joints from the robotic construction kit. The wrist and gripper modules are both made to snap onto a free voxel face. A carrier robot initially picks up one of the first three-component kinds, then maneuvers to connect wrists and grippers to the base part before placing it in the assembly, a process known as accessorizing.
The team believes that these robot swarms have a wide range of possible applications in sectors that now demand huge capital investments for permanent infrastructure or are infeasible. These include seismic metamaterials, automotive assembly lines, aircraft components, and airframes.
While the currently described algorithms are centralized, MIT also noted in their paper that if the system size increases, scalable compilers, and decentralized control mechanisms would be required. Although these algorithms gave useful examples, they were not demonstrated to be the best options. More advanced path planning and collision avoidance strategies could be used to shorten the construction period, and exploring the number and location of pickup stations is a crucial design factor that significantly influences the throughput of the robots. Further, the team will continue their work to ensure the continuity of metamaterial behavior in structures with greater performance.